Speakers
Arnoud Herremans, Lean Kaizen Consultant,The Netherlands
Henny Koch, Qimp Management Systems, The Netherlands
Dorthe Christina Kroun, Bavarian Nordic A/S, Denmark
Dr Daniel Marquardt, Boehringer Ingelheim, Germany
Dr Ann McGee, McGee Pharma International,Ireland
Objectives
This 2-day Master Class brings together well-experienced experts to discuss the latest expectations and requirements for Quality Metrics and KPIs and how they are linked to Continual Quality Improvement (CQI) and Business Continuity. This will support you turning your company’s quality excellence goals into reality.
Background
To remain ‘regulatory compliant’ and to ensure the continuity of product supply in a cost-effective way, systems and processes must be evaluated and the respective processes simplified and controlled. Important tools in this context are accurate Quality Metrics, the right Key Performance Indicators (KPIs) and Continual Quality Improvement.
Quality Metrics in itself are not new, though. They have already been used in pharmaceutical industry for years – even though mainly internally to measure operational performance. But quality can be measured on different levels and for many processes. Done in the right way, Quality Metrics can enable companies to reach a high quality performance. They will benefit from a continuous improvement in both operational performance and GMP compliance. And both are important for the continuity of business and product supply.
Now, the U.S. FDA has set up an initiative to use Quality Metrics for risk based inspections and published a draft Guidance for Industry in July 2015. In Europe agencies also use Quality Metrics. They are aiming to help regulators to separate manufacturing sites with poor standards from those continuously working on quality improvement.
In the end Quality Metrics will enable companies and regulators to benefit from a continuous investment in GMP to guarantee a high quality performance and the continuity of quality product supply.
Target Group
Managers and Executives from pharmaceutical Quality Assurance and Quality Management but also Business Executives and Production Managers and those involved managing the continuity of product supply.
Programme
Quality Metrics and beyond
- FDA’s Quality Metrics Initiative
- Expectations in the EU
- Quality Culture as the basis for quality improvements
- How to involve the management in Quality Metrics
- Set up of a practical review system
- Follow up actions on management reviews
- Understanding critical processes & where quality risks lie/ process mapping
- Defining the right KPIs
- Meaningful metrics (and the pitfalls)
- The role of Quality Impact Assessment & effectiveness checks
- The link to Opportunities for Improvement (OFIs), Continuous Quality Improvements (CQIs) and Business Continuity
- Process Analysis
- Root Cause Analysis
- Cause-and-Effect Diagrams
- Risk Assessment
- Quality Cockpit
- KPIs
- Tracking & Trending
- The importance of proper use and relevance of lagging and leading KPIs in correlation with process controls.
- The set up and implementation of a risk based data evaluation methods for continual improvement and the Management Review
- What do the numbers tell us?
- Business culture
- Empowerment of people
- How to shift individuals, teams, and organisations from a current state to a desired future state
- How to organise processes to empower employees to accept and embrace changes in their current business environment
- 8 Steps of Change (Kotter)
- True understanding of the quality risks specific to our businesses
- A shift to pro-active QRM from reactive risk assessment
- Integration of QRM and change management
- Moving away from the functional silo mentality
- Process and QMS improvement in the interest of patient care
- Meaningful performance evaluation criteria and metrics
- Why did we implement Metrics?
- How did we do it?
- What was the outcome?
- Lessons learned
- How to apply Quality Metrics as a Key Driver for CQI
Parallel sessions (2 out of 3)
1. Managing Data: The Bridge from Quality Metrics to CQI
Defining the right KPIs and Meaningful metrics (work on examples)
What to learn from the data
2. The new FDA Guideline on Quality Metrics – what is it all about?
Overview about the current status
Key areas and data to be submitted
How industry can prepare
The link to ICH Q12: Quality Metrics as part of Product Lifecycle Management
3. Analysis Tools for assessing and optimising Process Flows
How to choose and use the correct tools
You will be able to attend 2 of these sessions. Please choose the ones you like to attend when you register for the course.
This course is part of the GMP Certification Programme "ECA Certified Quality Assurance Manager" Learn more
This training/webinar cannot be booked. Send us your inquiry by using the following contact form.
To find alternative dates for this training/webinar or similar events please see the complete list of all events.
For many training courses and webinars, there are also recordings you can order and watch any time. Just take a look at the complete list of all recordings.
not available
not available
Not available
Please contact us:
Tel.: +49 6221 8444-0
E-Mail: info@gmp-compliance.org
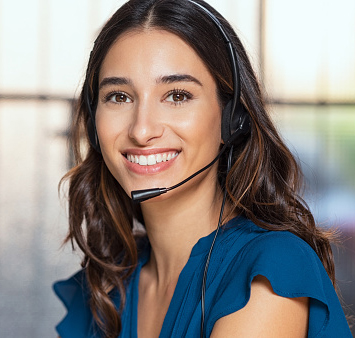
- Our Service
Testimonials
Your Certificate
Seminar Programme as PDF