This course is part of the GMP Certification Programme "ECA Certified Validation Manager" Learn more
This training/webinar cannot be booked. Send us your inquiry by using the following contact form.
To find alternative dates for this training/webinar or similar events please see the complete list of all events.
For many training courses and webinars, there are also recordings you can order and watch any time. Just take a look at the complete list of all recordings.
* also payable by credit card
Additional dates on-site
Additional dates on-site
not available
not available
Additional dates online
Additional dates online
not available
not available
Recording
Not available
Not available
Do you have any questions?
Please contact us:
Tel.: +49 6221 8444-0
E-Mail: info@gmp-compliance.org
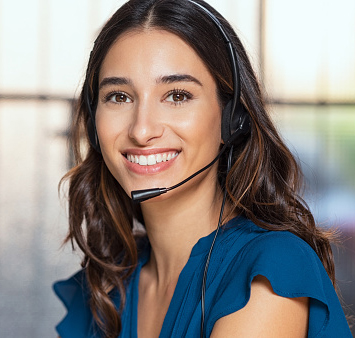
- Our Service
Testimonials
Your Certificate
Testimonials about our courses and conferences