Speakers
Dr Reinhard Adam, Berlin-Chemie
Dr Hiltrud Horn, Horn Pharmaceutical Consulting
Dr Afshin Hosseiny, ECA & Former Director QA at GSK
Dr Eva Keller, Ferring
Dr Jean-Denis Mallet, ECA & Former Head of the Pharmaceutical Inspection Dpt. AFSSAPS
Objectives
Learn how a successful and GMP-compliant process transfer should be conducted.
The key issues are the main topics of this course: development of a regulatory strategy, project management and monitoring as well as documentation of the transfer activities.
Background
The changing nature of the business strategies of pharmaceutical companies necessitates intra- and intercompany transfers of technology to create additional capacity for a new product, relocations of operations, site closures, and consolidations and mergers. Transfer of processes to an alternative site can occur at any stage in the product life-cycle, from development, scale-up, manufacturing, production and launch, to the post-approval phase.
Transfer of technology is a logical procedure that controls the transfer of any process together with its documentation and professional expertise between development and manufacture or between manufacturing sites.
At least the expertise from development, manufacturing, analytics, regulatory affairs, supply chain and engineering is necessary. This means that a transfer cannot be handled by a single-person. Therefore it is essential to build cross-functional transfer teams as a first steps in the transfer project. As interests and expertise are quite different within the team it is further essential to understand the project in its entirety and the tasks and deliveries of the single sub-teams. This is especially true for the transfer project leader.
The team is confronted with manifold issues. The process being transferred must be understood and sufficiently described – which can be a problem, especially for products from development or older products. But without this understanding the proof of equivalence after the transfer will never be successful.
In most of the cases the project is determined by the regulatory strategy. But Regulatory Affairs often finds that the filed process descriptions and the actual process in the donor site differ from each other. So transfer projects are very often also product maintenance projects. This costs time and money which both commonly were not budgeted.
The planned approach, the documentation of the transfer activities as well as written procedures are part of the EU GMP rules, as you can see, e.g., in chapter 7.4. Since 2010 Chapter 4 of the EU GMP guide has continuously been supplemented with new requirements on the documentation of a transfer and the requirements on written procedures for the execution of a transfer. But also without these demands from authorities: planning and documentation are the key factors for a successful transfer.
We want to give answers to questions like:
- What do agencies expect?
- How is the regulatory strategy developed?
- What are the milestones? How can the project be structured?
- What are the critical quality attributes in transfers of sterile or oral solid dosage form?
- How are process changes handled that are occurring during the transfer?
- What can a gmp-compliant documentation look like?
How can psychological problems in the transfer team be handled?
What can go wrong?
Target Group
This course addresses to staff from Production, Engineering, Quality Assurance, Regulatory Affairs and Project Management in charge of Transfer Projects. This involves Project Leaders and project team members, from receiving site as well as from donor site.
Participant comment:
"It was a very helpful training overall. Brought great discussion. This was a helpful exercise."
Sonya Meheux, Cytonet LLC
Programme
Fundamentals of Technology Transfer
- Pharmaceutical product life cycle and Technology Transfer
- Various types of transfer
- Regulation and GMP challenges for Technology Transfer
- Setting up the transfer team
- Identifying key elements of Technology Transfer
- What to consider when planning Technology Transfer
- Defining the transfer scope
- Identifying materials involved
- Defining the process, equipment and facility requirements
- Defining validation requirements
- Product hand over and completion of oral dose transfer
- Comparison of equipment and clean rooms / barrier systems of sending and receiving unit
- Critical quality parameters of product and process
- How to establish comparability criteria
- What is fixed and what can be changed: packaging material, process parameters, equipment, ... (?)
- Frequent failures & trouble shooting
- Scope of the Site Change
- Project Plan, Project Phases and Timelines
- Documentation of the transfer
- Regulatory Strategy (US)
- Unforeseen gaps
- Project Reporting
- Lessons learnt…
- Pre-requisites when considering an analytical method transfer
- Dealing with non-validated methods
- Why analytical methods should be transferred first?
- Is training of “receiving” analysts to be performed at “sending” site?
- Is the “5M” approach relevant for the transfer of analytical methods?
- How to fix the transfer strategy and establish a
- protocol (samples, materials, standards)
- Using ICH Q2 as a support for the transfer of an analytical method
- Comparison of results : what are acceptable criteria?
Developing a regulatory strategy for a site change
- Regulatory Guidance documents
- Differences EU, US, RoW
- Classification of transfers from a regulatory point of view
- Data & documents needed
- Timelines
- Costs
After having set up a regulatory strategy for a site change, most often further process and technology changes occur and become necessary for continuing with the transfer project.
- How to deal with this unplanned changes?
- Classification of changes
- How do this changes alter the overall strategy?
- Examples
- Setting up the project and the Transfer team
- Project Plan and Transfer Mater Plan: how to document the transfer activities
- Monitoring of the transfer activities
- Definition of milestones and time management
- Pre-evaluation and feasibility phase, preparatory phase, project completion phase
- Project Examples
- Defining documentation required pre-transfer
- Defining documentation required during the transfer
- Documentation required post transfer
- Roles and responsibilities of parties in preparation, review and approval of documentation
- Sign off and completion of transfer
- Reporting of transfer findings and change control
- How to manage the transition period (e.g. first few batches!)
- Roles and responsibilities of both parties
- Key challenges during the transfer (people and cultural aspects)
- What can go wrong?
Develop a Transfer plan – the objective of the workshop is to allow participant to practice developing a formal plan for a product transfer between two sites. Workshop participants will be provided with information about the product and its history, they will be asked to develop an appropriate transfer plan which includes sourcing of the materials, the validation plan, training at the new site, risk assessment and action planning. Additional information will be available if delegates request it to help them to develop the plan.
This course is part of the GMP Certification Programme "ECA Certified Technical Operations Manager" Learn more
This training/webinar cannot be booked. Send us your inquiry by using the following contact form.
To find alternative dates for this training/webinar or similar events please see the complete list of all events.
For many training courses and webinars, there are also recordings you can order and watch any time. Just take a look at the complete list of all recordings.
not available
not available
Not available
Please contact us:
Tel.: +49 6221 8444-0
E-Mail: info@gmp-compliance.org
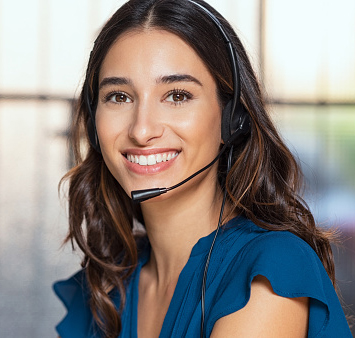
- Our Service
Testimonials
Your Certificate
Seminar Programme as PDF