All times mentioned are CET.
Objectives
CCI Testing
Different products and different container types require different testing methods: this event aims at giving an overview of the different CCI testing systems which are applied during production and as part of the quality control system. Apart from technical aspects the regulatory requirements on CCI testing will be highlighted as well as the applicability of inline and offline testing.
Visual Inspections Systems
Main topic of this course is the detection of defetcs like particles in injectables and their evaluation during batch release. Besides the current regulatory requirements with regards to particulate matter, routine 100% inspection of injectables will be addressed. Manual inspection as well as automated inspection systems will be covered, including validation, training, defect categories, AQL testing, trending and batch release considerations.
Different products and different container types require different testing methods: this event aims at giving an overview of the different CCI testing systems which are applied during production and as part of the quality control system. Apart from technical aspects the regulatory requirements on CCI testing will be highlighted as well as the applicability of inline and offline testing.
Visual Inspections Systems
Main topic of this course is the detection of defetcs like particles in injectables and their evaluation during batch release. Besides the current regulatory requirements with regards to particulate matter, routine 100% inspection of injectables will be addressed. Manual inspection as well as automated inspection systems will be covered, including validation, training, defect categories, AQL testing, trending and batch release considerations.
Background
CCI Testing
An intact container closure system, which is the sum of packaging components that protect the dosage form, is the pre-requisite for a safe and sterile drug product. The CC system protects the product from microbial contamination and also from exposure to gases or water vapour or the loss of solvent. Container Closure integrity testing is therefore a regulatory requirement and it is part of the whole life cycle of a sterile drug product.
Initially this testing was performed as part of the initial development of the packaging system and the system’s suitability verified in stability studies including on-going stability. Over the years, the expectation was raised to perform batch by batch verification with latest trends to 100% inline or offline testing wherever possible.
We will discuss and answer questions like:
- What are the current and upcoming GMP- and compendial requirements in the US / EU / RoW?
- Will container closure integrity testing change to 100% inline testing?
- What does the Annex 1 require?
- How do we have to define’ tight’?
- Which testing technologies are available and suitable?
- CCI testing of lyo & liquid vials
- CCI testing of ampoules
Visual Inspections Systems
In most cases particles found in parenteral medicines will lead to a quarantined product or even to the recall of the product – as we have seen in the last years in the cases of several pharmaceutical companies. Responsible staff in charge will have to start root cause analysis to find the source of the particles and will have to do an evaluation of batches already shipped.
There is still confusion within the global pharmaceutical industry with regard to the requirements for testing for visible particles. After the USP chapters <790> and <1790> were published, things have become much clearer, at least for the US.
There is still confusion within the global pharmaceutical industry with regard to the requirements for testing for visible particles. After the USP chapters <790> and <1790> were published, things have become much clearer, at least for the US.
In Europe the new chapter 5.17.2 of the European Pharmacopoeia now also gives further advice. However, many questions remain, e.g. concerning training, re-testing, detection capabilities and revalidation of inspection Systems.
Furthermore there has been a recognisable trend towards automated inspection machines throughout the last years. The challenge for pharmaceutical companies is to find a suitable machine for their products and to determine reasonable inspection parameters during qualification and validation. But also during routine process there are questions arising like re-testing and the usage of test-sets, doing AQL-Testing as well as the adjustment of parameters of the vision systems.
Furthermore there has been a recognisable trend towards automated inspection machines throughout the last years. The challenge for pharmaceutical companies is to find a suitable machine for their products and to determine reasonable inspection parameters during qualification and validation. But also during routine process there are questions arising like re-testing and the usage of test-sets, doing AQL-Testing as well as the adjustment of parameters of the vision systems.
We will address those topics during the conference and discuss and answer questions on
- The latest compendial requirements concerning particulate matter
- Compliance with the revised Annex 1
- Training and qualification of operators in the manual inspection
- Validation and operation of an automated inspection System
- Trending and monitoring of visual inspection data
- Correct AQL testing as part of the batch release
- Re-inspection of defect fractions
- Usage of artificial intelligence in visual inspection
Target Group
CCI Testing
This course is directed at specialists and executives from the areas engineering and production and QA dealing with the implementation and operation of systems for the container/closure-integrity testing of sterile medicinal products.
Visual Inspections Systems
Visual Inspections Systems
This course is directed at staff from sterile operations, that is production, quality assurance and engineering. But also suppliers of primary packaging materials and inspections technology are target group of this Event.
Technical Requirements
For our Live Online Training Courses and Webinars, we use Cisco WebEx, one of the leading suppliers of online meetings.
At http://www.webex.com/test-meeting.html you can check if your system meets the necessary requirements for the participation at a WebEx meeting and at the same time install the necessary plug-in. Please just enter your name and e-mail address for the test. If the Installation is not possible because of your rights for the computer system, please contact your IT department. WebEx is a standard nowadays and the necessary installation is fast and easy.
At http://www.webex.com/test-meeting.html you can check if your system meets the necessary requirements for the participation at a WebEx meeting and at the same time install the necessary plug-in. Please just enter your name and e-mail address for the test. If the Installation is not possible because of your rights for the computer system, please contact your IT department. WebEx is a standard nowadays and the necessary installation is fast and easy.
Programme

Seminar Programme as PDF
Container Closure Integrity Testing of Parenterals
Container Closure Integrity Testing of Sterile Drug Products – Requirements, Expectations and Exaggerations
Container Closure Integrity Testing of Sterile Drug Products – Requirements, Expectations and Exaggerations
- Container Closure Integrity during development, qualification and stability testing
- Regulatory, Pharmacopoeial and GMP requirements
- System integrity versus container damages
- Patient risks – do we need batch by batch testing?
- Industrial best practices
Container Closure Integrity Testing of Parenterals – a GMP inspector‘s View
- Applicable regulations & guidance
- Implementation of current requirements
- Expectations of a GMP-Inspector in GMP Inspections
- Examples of observations
Overview of Container/Closure Integrity Testing Technologies
The presentation gives a complete overview of the different aspects of leak testing to do CCIT in the pharmaceutical production. The systems presented can be used for the CCIT of vials, ampoules, syringes, BFS, IV bags, blisters etc.
- Leak, leak rate and the relevant physical units
- Leak test methods
- Pressure change methods (vacuum, pressure and LFC)
- Head Space Analysis using TDLAS
- Helium Leak Test and other Mass Spectroscopy Systems
- High Voltage Leak Detection (HVLD)
- Force Sensing Technology
- Capabilities and examples of the different methods
- How to select the right method
- How to generate positive controls
Case Study: 100% Testing of Vials
- System Setup
- Validation
- Routine operation
100% inline CCI Testing of Ampoules
- High Voltage inline testing: method description
- Integration in the production process
- Limits of the System
- Qualification of the System
- Validation
- Routine Operation
Visual Inspection Systems
Regulatory Requirements for the Visual Inspection of Parenterals
Regulatory Requirements for the Visual Inspection of Parenterals
- Compendial Requirements
- 100% visual inspection & AQL testing
- PharmEur, USP, JP - similarities and differences
- News from the Annex 1 revison
- Risk Management Considerations
Visual Inspection of Parenterals – a GMP Inspector‘s View
- Applicable regulations & guidance
- Current requirements for pharmaceutical industry
- Expectations of a GMP-Inspector
- Examples of observations
Manual Visual Inspection – Theory and Practical Aspects
- Probabalistic nature of visual inspection
- Defect categorisation
- Differentiation of test kits for training, qualification and Routine
- Qualification and training of personnel
- Standardisation of working conditions in Manual inspection
- Usage of the Knapp and the modified Knapp test
Automated Visual Inspection – from Setup to Routine Use
- Limitations of automated inspection
- Setting up a qualification strategy for automated Systems
- Cross validation during the PQ phase of an automated System
- Importance of particle detection rates
- System suitability, requalification and revalidation
- Inspection of eject fractions
- The Roche Inspection systems: manual, semi-automated and fully automated inspection
Requirements, Composition, and Handling of Test Sets
- Definition of defect categories
- Set-up and composition of a test set
- Test sets and their use for training, qualification and Routine
- Handling and release of test sets
- Documentation
Re-Inspection of Defect Fractions in Visual Inspection
Different scenarios will be covered such as:
- Re-inspection or additional inspection of “grey-channel” units from (semi-) automated inspection
- Re-inspection in case of exceeding alert limits or AQL failures
- Focused re-inspection
- Inspection approaches in case of investigations due to unexpected particles (e.g., to determine frequency of occurrence of visible particles when particles are found during release/stability testing
Automated Visual Inspection Based on Unsupervised Machine Learning
- Vector segmentation using unsupervised machine learning
- Characterizing variation using computer Vision
- Learning normal variation in defect-free bottles
- Visual inspection via anomaly detection
Particle Testing and the Correlation with Trending and Batch Release
- Why do we Monitor (What is it all about)
- Data and measurement
- The AQL trap
- Improvement process map
- Investigation and routine analysis,
- Release Process. “To AQL or not to AQL that is the Question”
- Product release: “Falling off a log”
This course is part of the GMP Certification Programme "ECA Certified Technical Operations Manager" Learn more
This training/webinar cannot be booked. Send us your inquiry by using the following contact form.
To find alternative dates for this training/webinar or similar events please see the complete list of all events.
For many training courses and webinars, there are also recordings you can order and watch any time. Just take a look at the complete list of all recordings.
* also payable by credit card
Additional dates on-site
Additional dates on-site
not available
not available
Additional dates online
Additional dates online
not available
not available
Recording
Not available
Not available
Do you have any questions?
Please contact us:
Tel.: +49 6221 8444-0
E-Mail: info@gmp-compliance.org
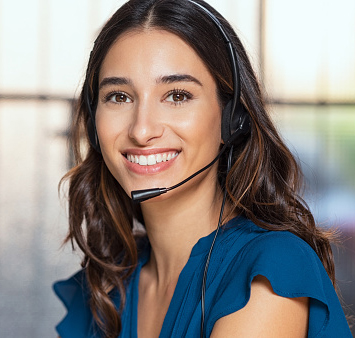
- Our Service
Testimonials
Your Certificate
Seminar Programme as PDF
Testimonials about our courses and conferences